Configuring an AI model pipeline to detect robotic grasping anomalies in real time
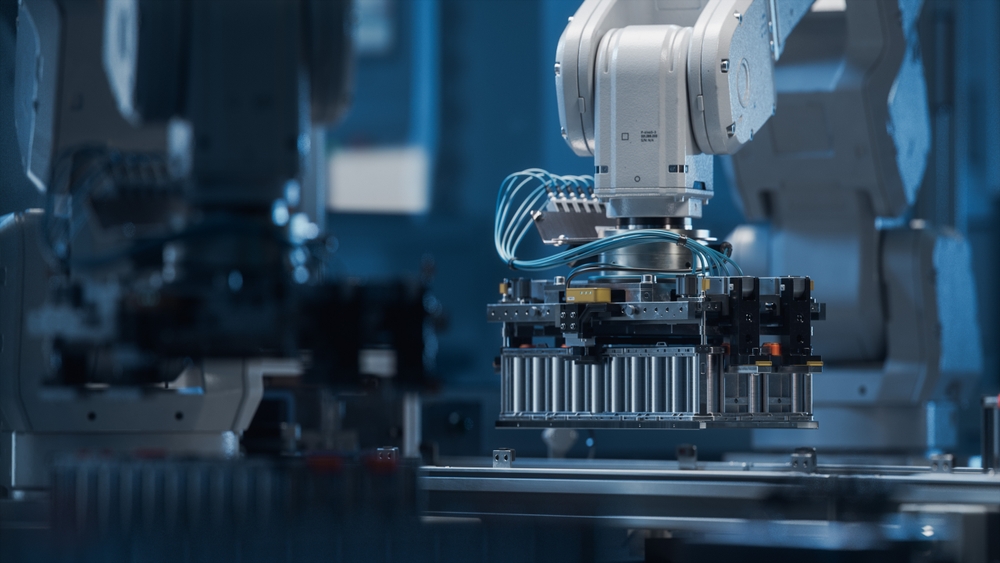
Challenge
- Robot drops battery, causing downtime
- Difficulty utilizing existing machine learning solutions due to ‘class imbalance’ problem
- Difficulty treating footage with no battery for the robot to grab in the first place as separate normal data
Approach
- Train a model with only normal data using the Anomaly Detection algorithm
- First, the Object Detection model classifies cases where there is no battery for the robot to grab as normal data.
- The Anomaly Detection model then detects anomalies and sends a warning alarm when the robot fails to properly grab a battery.
Result
- Successfully implemented real-time anomaly detection (99.9% accuracy)
Full Story
Need a tool that can learn and infer one-in-a-million anomalies
Smart factories use various automated robotic arms. For example, in a factory producing cylindrical rechargeable batteries, robotic arms may handle dozens of batteries to ensure smooth flow from the initial stage to the final product.
Occasionally, the robotic arm malfunctions. It might report moving a million batteries but only handle 999,999. If one is dropped, production must halt to locate the missing battery.
However, having a third shift to monitor rare events is impractical. Training an AI model is also challenging as it needs a mix of normal and abnormal data, and in this case, abnormal data is scarce. This problem, which is common in industry, is called “class imbalance”.
- Class imbalance: Categories of data, such as ‘normal’ or ‘abnormal’, are called classes, and a large difference between the number of normal and abnormal data is called class imbalance. In a supervised learning model, it is difficult to train a model properly if there are too few abnormal data. For this reason, methodologies such as unsupervised learning models have been proposed that can train a model using only normal data.
Configure AI model pipelines to meet all your inspection needs
LISA, an industrial AI solution from AHHA Labs, performs anomaly detection using video data. The Anomaly Detector, a deep learning algorithm, identifies all non-normal states, known as anomalies. It effectively catches outliers. By training solely on normal data and measuring deviations from the normal data distribution, it overcomes the class imbalance problem in industrial settings.
To address pain points at Company D, a producer of secondary batteries for electric vehicles, LISA analyzed video footage of a robotic arm handling a secondary battery.
If the robotic arm failed to grip the battery correctly due to an error, a heat map was generated, indicating the extent of the anomaly from the normal state.
One more requirement. LISA had to recognize that having no batteries to move at all was a normal situation.
If trained solely on normal data, LISA’s anomaly detection model would incorrectly identify a situation with no batteries to grab (a normal condition) as abnormal, as it was trained only on scenarios where the maximum number of batteries were handled. To solve this problem, we would have to train on all cases where there were no batteries to grab, labeling them as normal data, but this solution is too difficult.
To address this issue, we introduced the Object Detection algorithm, a deep learning method that locates each object within a bounding box and classifies them as normal or abnormal. Before detecting an anomaly when a robot arm grabs a battery differently than usual, it can determine if there is a battery to grab in the first place.
Stop battery fires and downtime from happening
In tests against a variety of anomalies, LISA detected 100% of anomalies. The benefits are clear. It’s a very small chance, but when it happens, the damage is huge: not only do you have to stop production, but you don’t know how long it will take to find the missing batteries. Even worse, a battery rolling around the manufacturing floor could catch fire and cause even more damage.
The AHHA Labs team will continue to focus on our customers’ pain points and move from the impossible to the possible.
AI Inspection with 86% Cost Reduction Using On-Device AI
Challenge Defects caused by external contaminants are unpredictable in shape, making rule-based algorithms ineffective—necessitating a deep learning model...
Transforming Battery Manufacturing with AI Inspection & Data Automation
From Manual Inspections to Smart Factories: The Evolution of Battery ProductionWith the rapid expansion of the electric vehicle (EV) market, the...
A 3-Step AI Inspection Pipeline for Rubber Sheet Defects: Automating Detection, Classification, and Location Analysis
Challenge In the tire manufacturing process, rubber sheets produced during the calendering process lacked an automated quality inspection system and relied...
Boosting Control Efficiency of Battery Assembly Lines by 300% Through a Remote Monitoring System
Challenge The assembly lines for EV batteries are massive and highly complex, requiring multiple personnel to monitor equipment status and respond to alarms....
Detecting Inspection Data Drift Caused by Material Changes: A Case Study on the Data Quality Index (DQI) Model
Challenge In manufacturing, consistently capturing high-quality optical images is essential for training machine learning models and ensuring high...