Data Integration: Managing Inspection Data by Barcode Number for a Secondary Battery Manufacturer with Data CAMP
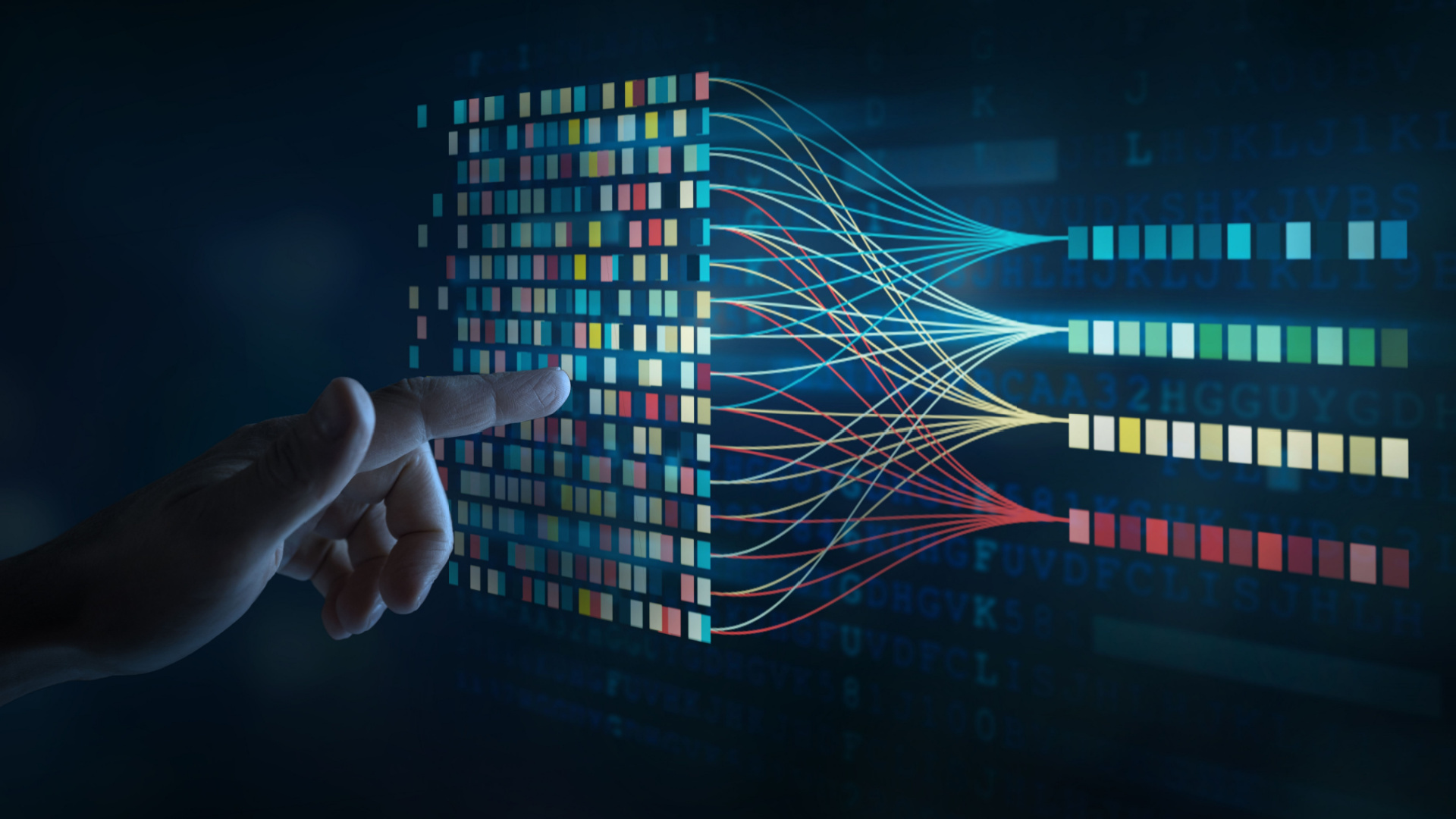
1. Challenge
Lack of a production history management solution to manage product inspection data by barcode number
In 2015, the introduction of the 21700 cylindrical battery marked a significant advancement in battery technology. This newer battery type, characterized by increased energy density and capacity, has become a standard in many electric vehicles, surpassing the previously prevalent 18650 batteries. However, the existing production line for 18650 batteries presented challenges for production management.
The issues primarily stemmed from an outdated defect inspection system and the lack of integration and linkage in data management. For instance, the unique barcode assigned to each battery and various inspection data were collected independently, leading to an inability to manage production history effectively. The result was a fragmented system that hindered comprehensive oversight and analysis of the manufacturing process.
2. Background
Minimize the impact on public safety caused by defective batteries and mitigate the financial repercussions associated with costly product recalls.
Potential issues were manageable when employing 21700 batteries in small power tools and laptops. However, the dynamics shift significantly when these batteries are integrated into electric vehicles (EVs). Unlike smaller applications, EVs incorporate a larger quantity of batteries, and a single failure could result in loss of life, not to mention substantial costs associated with recalls.
To prevent the recurrence of such issues, it is crucial to trace and identify batteries with previously overlooked defects. Unfortunately, without integrated inspection data, achieving traceability becomes exceedingly challenging.
Company A, one of the world’s leading companies of secondary batteries for electric vehicles, has been AHHA Lab’s customer for many years. They are satisfied with using AHHA Lab’s Data CAMP solution for collecting and storing comprehensive inspection data and real-time monitoring of the entire inspection process. But we also found that they were apprehensive about the increasing number of EV fire cases in recent years, and still did not find a good way to manage the inspection history.
Why is it so Difficult to Integrate Data on the Manufacturing Floor?
One of the challenges in existing manufacturing environments arises from the prevalent use of inspection equipment that operates on a ‘controller’ type rather than a PC-based system. For instance, vision controllers are camera-based devices that capture images of the surface of the produced items and notify deviations from predefined rules. However, these controller-type inspection devices typically only transmit data on the presence or absence of defects, lacking the capability to handle external information such as barcode numbers of the inspected products. In other words, vision controllers may not be aware of which cell the inspected item belongs to. While developing separate software is a possible solution, the nature of commercial inspection equipment makes processing external information a burdensome task, potentially leading to a slowdown in the manufacturing process or errors.
3. Solution
Unifying Inspection Data and Barcodes through Data CAMP
AHHA Labs undertook the challenge of enhancing the Data CAMP solution to address this issue. We seamlessly integrated the inspection data generated by all inspection equipment with unique barcode numbers throughout the entire process. Additionally, we developed an automated preprocessing solution that effortlessly collected and uploaded the data to a higher-level server in the desired format. Now users can easily access comprehensive inspection data for each battery in a single view.
Here’s how it operates: The programmable logic controller (PLC) simultaneously transmits a code to both the inspection equipment and Data CAMP to initiate the inspection. Data CAMP receives a unique barcode number in conjunction with this process. When the inspection machine generates defect presence data, Data CAMP combines the inspection data with the unique barcode number and forwards it to the manufacturing execution system (MES) and upstream servers. This sequence is repeated for each inspection machine, ensuring a streamlined and efficient process.
Data CAMP is designed to accommodate various types of inspection equipment and diverse data formats. With an impressive 99.9% success rate in data integration, in the event of a future product issue, the collected data can be effortlessly traced back to the production process. This facilitates prompt identification of the problem and enables swift improvements.
AHHA Labs is poised to assist you in the effective implementation of a data-driven manufacturing approach by promptly addressing the specific requirements of the field.
Explore various solutions to facilitate the digital transformation of manufacturing processes.
📌 Mastering Real-Time Anomaly Detection with LISA: Your Gateway to Industrial Excellence
📌 Why DATA CAMP Is the Ultimate Choice for Digital Twins
📌 Embracing the Future: Why DATA CAMP Outshines Traditional SCADA